what is compressed air energy storage system?
what is compressed air energy storage system? The purpose of this article is concerned with the power storage at a greater life span without using a battery. This prototype is a mini power plant used to store power for later use when there is no sunlight and also where no transmission lines are available, such as Urban areas or deserts. It gives us a better opportunity to overcome the battery issues.
As electricity is the basic need of humanity, sometime we ignore the natural sources surrounding us have the strongest power to full-fill our needs. Here we use solar plates to capture solar energy and a CAES system to store this energy for later use. Later this energy can be used to light-up over homes.
This is a prototype of a power generating and storage system. It uses solar power for energy production. The major parts used in this project includes
1- Solar panel or a Power Supply
2- Air Compressor
3- Air Tank
4- Turbine
5- Generator
6- Load
To gain practical knowledge of engineering field is soul of engineering career. One can be benefited from by working on a project and reading research papers to get up-to-date knowledge related to the field. As my project deals with the up-coming electrical issues, End of water, Expensive turbines, and short life time of batteries.
This project introduces a energy storage without any battery and have a Life span up-to 80 years.
Our lives have become so robotic, that we want machines to do our part of work. By doing this a lot of pollution and drawbacks are created which we ignore. But this project is free from such problems.
As the battery has shorter life time up-to 1 year, this prototype presents an alternative to the battery.
The ability to efficiently harness and utilize renewable but intermittent energy sources such as solar, wind and geothermal for electrical power production, is critically dependent on the availability of cost-effective, energy-storage technologies. Existing storage technologies include electrochemical batteries and fuel cells, super capacitors, thermal-storage materials, fly-wheels, pumped- hydro (PH), superconducting magnetic energy storage etc. So far, to the best of our knowledge, there have been no concerted efforts to examine smaller scale CAES systems as effective storage solutions for renewable energy sources.
Specifically, SS-CAES can be effective energy storage solutions. When used in conjunction with photovoltaic panels, where air-compression is powered by the PV panel(s) during the day and energy extraction (via appropriate pneumatic to electrical energy via turbines) occurs during PV inactivity. We propose to examine the viability of a unique energy-efficient, small-scale, compressed-air energy storage system that can be specifically tailored to power household appliances, and the scalability of such systems to power individual household and commercial use. As it is a prototype and is beneficial if an effort is applied to it in future. It also had a friendly environment towards nature. It provides a lifetime up-to 80 years whereas a battery needs maintenance each year.
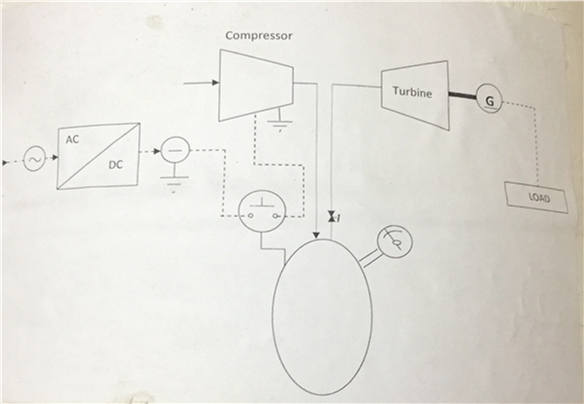
The power supply that is used in the project drives an output of 25 Amp DC to run the compressor. We can also use solar panel instead of power supply to store the energy for compressor working.
The purpose of power supply is to convert 220V of AC to 25 Amp of DC voltages as required.
What is Tripping Relay?
Tripping relay is located on the Air tank. The function of this relay is to maintain a pressure on the tank. It is normally set to a point 75 PSI (pressure per square inches). It also had a knot in-order to maintain pressure. The pressure can be Increases when the knot is Open, and decreases pressure value when the knot is kept closed. Air Compressor, a double cylinder air compressor is used for air compression. Its process time is nearly 15 mints, it gets heat-up after that and takes rest for good quality of service.
Turbine, the compressed air further moves to the turbine and make the turbine to work.
Generator, the generator is driven by the turbine. It gives us an output of 12V at output.
Compression of air creates heat; the air is warmer after compression. Expansion removes heat. If no extra heat is added, the air will be much colder after expansion. If the heat generated during compression can be stored and used during expansion, the efficiency of the storage improves considerably. There are three ways in which a CAES system can deal with the heat. Air storage can be adiabatic, diabetic, or isothermal.
One implementation of isothermal CAES uses high, medium and low pressure pistons in series, with each stage followed by an air blast venture pump that draws ambient air over an air-to-air (or air-to-seawater) heat exchanger between each expansion stage. Early compressed air torpedo designs used a similar approach, substituting seawater for air. The venture warms the exhaust of the preceding stage and admits this preheated air to the following stage. This approach was widely adopted in various compressed air vehicles such as H. K. Porter, Inc.’s mining locomotives and trams. Here the heat of compression is effectively stored in the atmosphere (or sea) and returned later on.
Limitation
Air tank limitations
The air tank is limited to 75 PSI pressure above this pressure the switching relay automatically turn off the compressor. The relay is set for this function.
Air Compressor
Type: 2 Cylinder, air compressor
Mode # Ac808
Voltage 110V
Max. Pressure 150 PSI
Duration 12 – 15 minimum
Displacement 70 L/Min
Turbine bladed turbine and generator
1500 RPM (revolution per minute)
Safety
Air tank
- Pressure should not be exceed from set
- The selected pressure would be less than, maximum capacity of the tank.
- Before starting the procedure one should check all the knots of air tank.
Air Compressor
- Small size and weight.
- Don’t required separation cooling system.
- Compact size and complete packages.
- Vibration free operation does not require special foundation.
- Relative first cost improves as size increase.
- Don’t require any special foundation.
- This air compressor is equipped with thermal overload protector. If unit shut off automatically during operation, do not attempt to restart compressor. Turn compressors ON/OFF switch to test OFF position. Allow Compressor to cool off. For approximately 15 mints before resuming use.
- Each successive so that no more than 15 to 20 mints machine cylinder fever, weight until the machine cylinder is not hot and then continue to use.
- Minors can’t use this product.
Pneumatic System
A pneumatic system is a system that uses compressed air to transmit and control energy. The advantages of pneumatic systems are Pneumatic control systems are widely used in our society, especially in the industrial sectors for driven of automatic machines. Pneumatic systems have a lot of advantages.
(i) High effectiveness
Many factories have equipped their production lines with compressed air supplies and movable compressors. There is an unlimited supply of air in our atmosphere to produce compressed air. Moreover, the use of compressed air is not restricted by distance, as it can easily be transported through pipes. After use, compressed air can be released directly into the atmosphere without the need of processing.
(ii) High durability and reliability
Pneumatic components are extremely durable and can-not be damaged easily. Compared to Electro-motive components, pneumatic components are more durable and reliable.
(iii) Simple design
The designs of pneumatic components are relatively simple. They are thus, more suitable for use in simple automatic control systems. Technological Studies Pneumatic Systems
High adaptability to harsh environment
Compared to the elements of other systems, compressed air is less affected by high temperature, dust, corrosion, etc.
Safety
Pneumatic systems are safer than electromotive systems because they can work in inflammable environment without causing fire or explosion. Apart from that, over-loading in pneumatic system will only lead to sliding or cessation of operation. Unlike electromotive components, pneumatic components do not burn or get overheated when over-loaded.
Easy selection of speed and pressure
The speeds of rectilinear and oscillating movement of pneumatic systems are easy to adjust and subject to few limitations. The pressure and the volume of air can easily be adjusted by a pressure regulator.
Environmental friendly
The operation of pneumatic systems do not produce pollutants. The air released is also processed in special ways. Therefore, pneumatic systems can work in environments that demand high level of cleanliness. One example is the production lines of integrated circuits.
Economical
As pneumatic components are not expensive, the costs of pneumatic systems are quite low. Moreover, as pneumatic systems are very durable, the cost of repair is significantly lower than that of other systems.
Limitations of pneumatic systems
Although pneumatic systems possess a lot of advantages, they are also subject to many limitations.
Relatively low accuracy
As pneumatic systems are powered by the force provided by compressed air, their operation is subject to the volume of the compressed air. As the volume of air may change when compressed or heated, the supply of air to the system may not be accurate, causing a decrease in the overall accuracy of the system. Technological Studies Pneumatic Systems
Low loading
As the cylinders of pneumatic components are not very large, a pneumatic system cannot drive loads that are too heavy.
Processing required before use
Compressed air must be processed before use to ensure the absence of water vapor or dust. Otherwise, the moving parts of the pneumatic components may wear out quickly due to friction.
Un-even moving speed
As air can easily be compressed, the moving speeds of the pistons are relatively uneven.
Noise
Noise will be produced when compressed air is released from the pneumatic components.
Main pneumatic components
Pneumatic components can be divided into two categories:
- Components that produce and transport compressed air.
- Components that consume compressed air.
All main pneumatic components can be represented by simple pneumatic symbols. Each symbol shows only the function of the component it represents, but not its structure. Pneumatic symbols can be combined to form pneumatic diagrams. A pneumatic diagram describes the relations between each pneumatic component, that is, the design of the system
Safety measures when using pneumatic control systems
(a) Compressed air can cause serious damage to the human body if they enter the body through ducts like the oral cavity or ears.
(b) Never spray compressed air onto anyone.
(c) Under high temperature, compressed air can pass through human skin.
(d) Compressed air released from the exhaust contains particles and oil droplets, which can cause damage to eyes.
(e) Even though the pressure of compressed air in pipes and reservoirs is relatively low, when the container loses its entirety, fierce explosions may still occur.
(f) Before switching on a compressed air supply unit, one should thoroughly inspect the whole circuit to see if there are any loose parts, abnormal pressure or damaged pipes.
(g) A loose pipe may shake violently due to the high pressure built up inside it. Therefore, each time before the system pressure is increased, thorough inspection of the entire circuit is required to prevent accidents.
(h) As the force produced by pneumatic cylinders is relatively large, and the action is usually very fast, you may suffer serious injuries if you get hit by a cylinder.
(i) Switches should be installed on the compressed air supply unit to allow easy and speedy control of air flow.
(j) In case of a leakage, the compressed air supply unit should be turned off immediately.
(k) The compressed air supply unit must be turned off before changes can be made to the system.
(l) Stay clear of the moving parts of the system. Never try to move the driving parts in the mechanical operation valve with your hand.
Also read here