Introduction to the problem
How electrostatics is used to encapsulate drugs in different industries?. This paper presents viable perspectives of generation of polymeric particles stacked with a sedate by electro-hydro-dynamic atomization(EHDA). Particles were created from paracetamol (4-acetamidophenol) , budesonide and polylactic corrosive containing Taxol (paclitaxel). Impact of dissolvable sort and vanishing rate, as well as other polymers added substances on molecule morphology and sedate discharge rate is illustrated It is appeared that rapidly vanishing solvents have a propensity to make empty particles. Sedate discharge rate from empty particles is considerably higher than from strong ones. Expansion of water-soluble polymer, polyethylene glycol, too increased at sedate discharge rate
From igniting fire using stones to asking Alexa to switch on the lights, man has paved his way to the modern era through several years of technological advances. The first man to see the lightning might have got scared and would have thought about electrostatics for once. It was mostly a fear at first, but curiosity eventually won out, and we began to explore, examine, and, eventually, apply electrostatics. Since then, electrostatics has been doing wonders and expected to do more in the future. Atomization of liquids is also one of the applications of electrostatics. When a droplet of liquid is exposed to a high electric field, the mutual repulsion of electrical charges within the droplet causes it to deform to a conical shape. If the electric field is powerful enough, a thin liquid jet arises from the cone’s apex, which quickly breaks up into a mist of fine droplets. Such a spraying technique using electrostatics is called Electro Hydro Dynamic Atomization (EHDA) method. Lets study about electrostatics to encapsulate drugs in different industries.
Methodology
Microencapsulation is defined as the process of enclosing micron-sized particles of solids or droplets of liquids or gases in an inert shell, which separates and provides protection them from the surrounding environment while also controlling the drug release profile. The system consists of an electrically conducting nozzle attached to a high voltage power supply, as well as a liquid supply system, typically a syringe pump. A ring linked to the intermediate voltage is often placed below the nozzle to stabilize the method. Because of the mutual repulsion of electrical charges in the liquid droplet, it has a conical shape from which a liquid jet arises at the apex. This liquid filament falls away into drops. Multiple forms of the atomization process can be noted depending on the voltage applied, liquid characteristics, and liquid flow rate. Two modes of EHDA operation are of significance for drug microencapsulation: cone-jet mode and micro-dripping mode. The figure shows both modes: cone-jet on the left side and micro dripping mode on the right side.
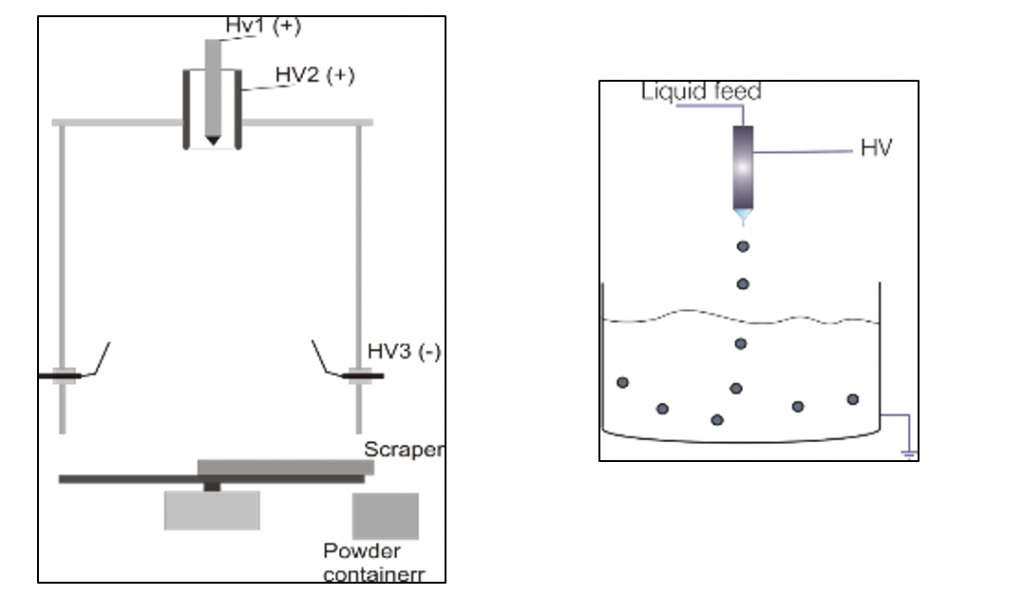
The first reactor, which runs in cone-jet mode, generates small highly charged droplets. It runs at approximately 11kV main voltage (HV1) and 8 kV additional stabilizing voltage (HV2). The polymer – drug solution is delivered to the nozzle at a rate of 2 ml/h. Droplets must be released in order to prevent Rayleigh explosions and make them controllable. Corona electrodes connected to the opposite voltage (HV3, -5kV) are used to perform droplet discharge. To ensure complete droplet discharge, the discharge current should be 2-3 times higher. The rotating electrostatic precipitator collects dry particles. This modern EHDA powder production reactor is stable and produces a few grammes of almost mono-disperse particles per hour. There are no discharge electrodes in the second reactor because the particles are much larger and have lower electrical charges. The reactor operates at a flow rate of 1-5 ml/h and a nozzle potential of 2 kV. As a nozzle, a blunt epidemic needle with a diameter of 0.5 mm was used. The diameter of the capsules can be changed by changing the flow rate and the volume.
Conclusion:
The capsules obtained by two different methods were different from each other. In comparison to the porous surface of the second type of particles, the surface of the particles obtained in the cone-jet type EHDA reactor is smooth. This is most likely due to the fact that wet particles in a micro dripping type reactor are immersed in a water solution. Water diffuses into the organic solvent and acts as an antisolvent, causing polymer precipitation. The drug release characteristics of these two types of particles are also distinct. These capsules are widely used in pharmaceutical, cosmetic industry, agrochemical and food industries, being used in flavors, acids, oils, vitamins, microorganisms. electrostatics to encapsulate drugs in different industries.
Future work:
In order to encapsulate drugs, alternative methods are being researched and discussed. Gravity and other natural forces are considered to be used to encapsulate drugs. Although, electrostatics is one of the best ways for drug encapsulation, but it is very costly. The new and latest technology has the capacity to coat drops with various layers, increased flexibility in terms of drop volume and shell materials, and the manufacturing of stronger and more stable capsules.
Also read here
https://eevibes.com/digital-logic-design/discuss-the-stimulation-study-of-elevators-control-system/