INTRODUCTION:
In this article I will describe how to perform Micro Particle Diameter Detection with Electrostatic Sensor for Powder Feeding Pipeline. During the transport of micro particles, the charge is induced by collision and friction, i.e., the powder feeding process during 3D printing of metal part. For the detection of the micro particle signals, characteristics of charging of particles play an important part. The charge on the micro particles can be detected by an electrostatic sensor. From the electrostatic sensor and the principle of charged particles in the feeding pipeline, the micro particles are weakly charged by the free-falling motion in the pipeline. There are two types of electrostatic sensors. The plug-in electrostatic sensor is not adapted to general situations. It can only detect micro particles within a few tens of millimeters of the metal. Therefore, this scheme is not satisfied. Inductive electrostatic sensors with high sensitivity and anti-interference are considered for adoption. The sensor is expected to detect the moving charges and not deposited. The conceptual model of the electrostatic sensor measurement system.
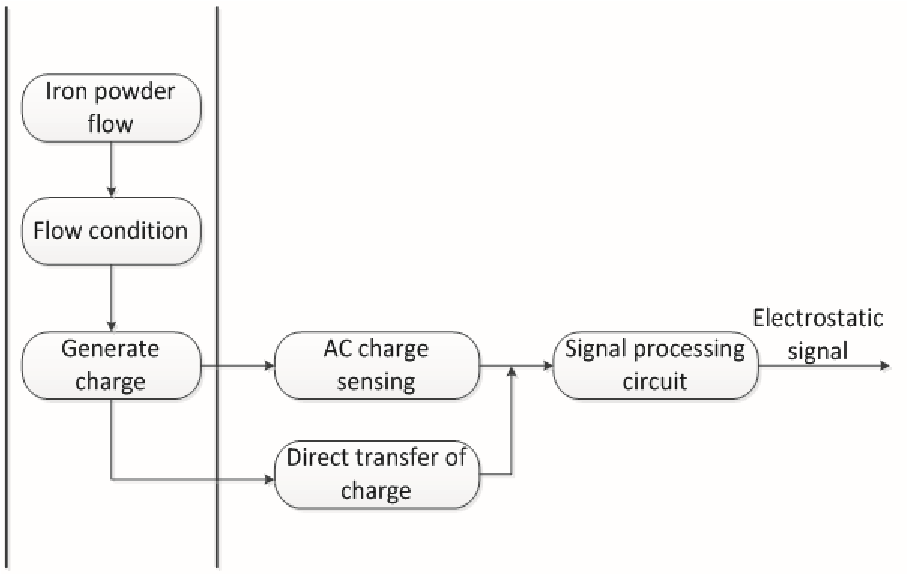
Electrostatic sensor detection system models. The charged particles flow through the electrostatic sensor during working. Due to the phenomenon of electrostatic induction, an equal amount of electric charge will be generated on the inner and outer surfaces of the sensor electrode. This situation causes that the quasi-electrostatic generated around the sensor is constantly changing. The induced charge and the induced potential generated are also constantly fluctuating. This is the basis for measuring the velocity and concentration of iron powder by inductive electrostatic sensors. The powder flowing parameters, such as velocity, concentration and micro particle diameter, are reflected by the fluctuation information of the induced charges. The parameters reflected can be obtained by the appropriate method of signal processing. Many advantages are in the electrostatic inductive sensor, including a simple structure, convenient and quick installation, high sensitivity, low price, convenient maintenance, safety and suitable for harsh environment. Therefore, it is widely used in powder signal parameter detection. The basic model of the proposed electrostatic sensor.
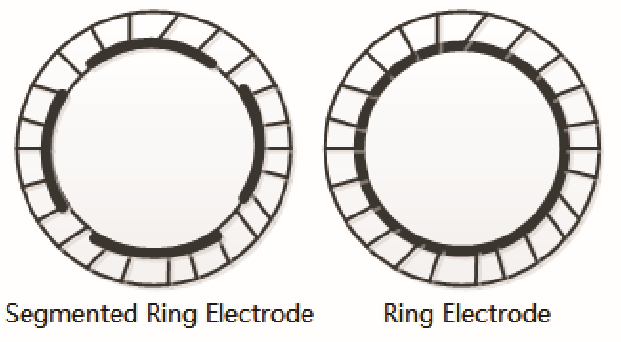
Methodology for Micro Particle Diameter Detection with Electrostatic Sensor
System modeling:
The method of installation is that the electrostatic sensor is put on the outer wall of the powder feeding pipeline directly. The powder feeding pipeline is wrapped around a grounded copper film as a shielding layer for measurement. The electrostatic sensor should be shielded and the case grounded. They can protect the detected signal from the interference of external signals.
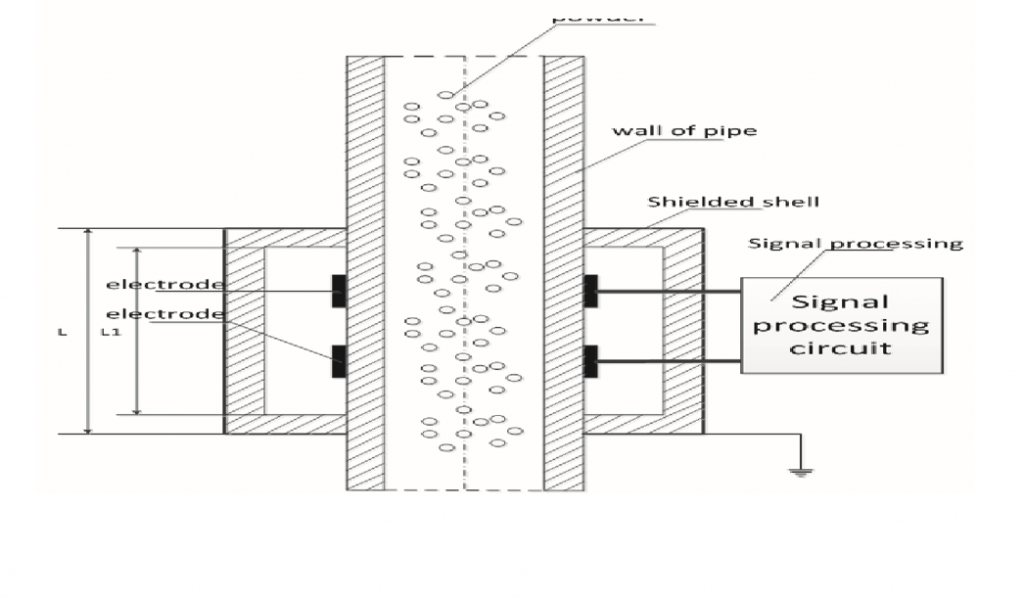
The electrodes of the electrostatic sensor are connected to the signal processing circuit. The capacitance between the electrodes and the pipe wall is insignificant. The electrostatic charge density is usually between 10-7C and 10-3C in the powder feeding pipeline. So, for the fluid with a mass flow of 0.3~3kg/s, the current amount is not more than 3mA. Compared to the induced charge, the electromagnetic generated by current can be ignored. It can be supposed that a particle carries a charge of –q which is moving axially at a specified velocity. That is equivalent to an impulse response to the sensing system. The response can be used to reflect the characteristics of the powder flow parameters.
Mathematical Modeling:
It is mainly to study the characteristics of induced charge q1 caused by the point charge -q on the inner surface of the electrode. The numberless charge in reality can be treated as an equivalent charge grounded electrical conductor, the electrostatic field around the electrostatic sensor will be formed. The axial width of the ring electrode is defined as w, the diameter is D, and the radial thickness can be negligible. Micro Particle Diameter Detection with Electrostatic Sensor.
A certain amount of static charge will be induced when the point charge passes through the ring-shaped electrostatic sensor by free fall. The extracted signal of electrostatic charge will be detected by this method.
Electrostatic Sensor Design:
The electrostatic sensor is more sensitive to particles near the pipe wall. The width of the sensor electrode and the ratio of the pipe diameter W/D play the essential role in the influence of consistency in spatial sensitivity. In other words, the spatial sensitivity increases as the ratio increases.
The ratio between width and diameter has a great effect on the spatial filtering characteristics of the sensor. After experiment, 1/9 is discovered to be the most suitable ratio in filtering as normal.
The sensor electrode characteristics, such as heat resistance, corrosion resistance and wear resistance, should be considered during the design of the sensor. Making the metal electrode highly sensitive to iron powder in the center of pipe is the same importance.
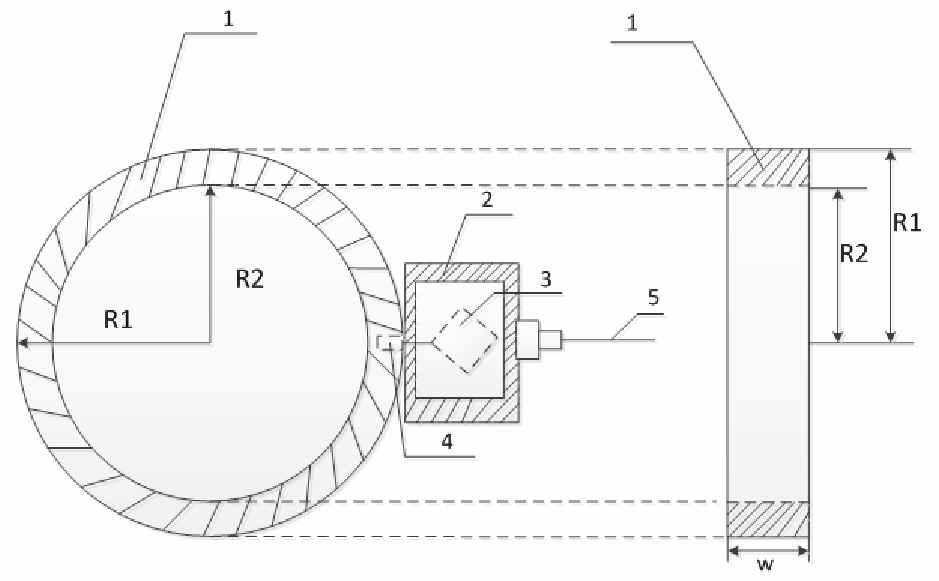
The number 1 is the electrostatic induction sensor electrode and electrode width. The number 2 is the amplifying circuit shielding shell. The number 3 is the circuit and signal processing unit. The number 4 is the sensor and circuit connection hole. The number 5 represents signal output cable. R1 is the outer radius of the electrostatic induction sensor electrode, R2 is inner, and W is the width. Assume that the induced charge of the powder charge on the electrode is q(t), and that the model of the output voltage is u(t).

Measurement:
Two similar signals are generated on the electrodes when the particles fall freely through the upstream and downstream electrostatic sensor electrodes. The method of signal process can detect the similarity between the two signals. The distance between the two sensors is existed. The delay time is calculated. The corresponding falling velocity can be obtained.
E=V/L (14)
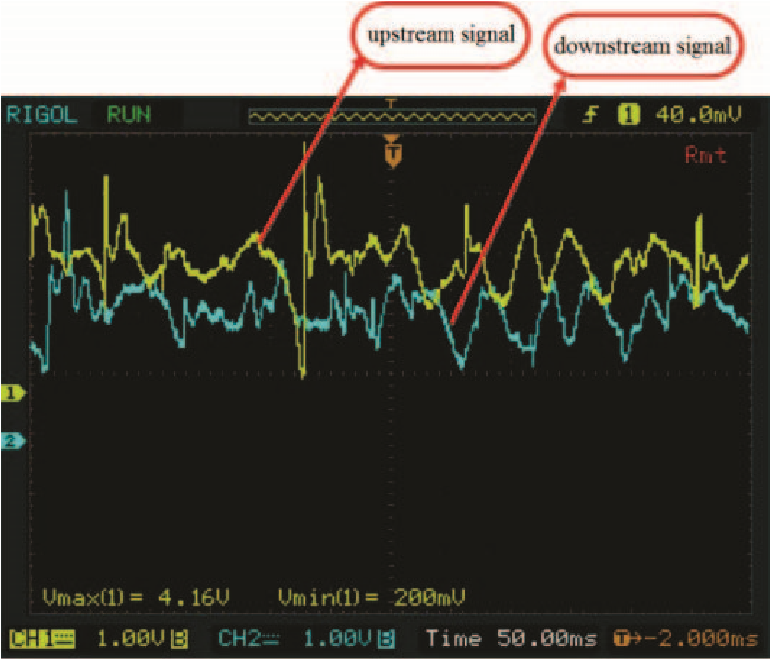
Conclusion:
- Micro particles with different diameter are used as experimental materials. The electrostatic signals of micro particles with three different diameters were detected at three different flow rates.
- Through the analysis of experimental data, it is verified that the power and main frequency of available signal are positively correlated with diameter and flow velocity of the micro particle.
- Through the design of the electrostatic sensor and the actual measurement accuracy of the sensor, we can draw some points.
- The structural design of electrostatic sensors should be in-depth study, such as choice of electrode width and material, design of shielded outer layer and feasibility in practical.
- The design of each link will affect the measurement accuracy of the sensor.
- In the research of the installation of the sensor in practical, the sensitivity of the sensor is relatively high when the ratio of the sensor electrode width W to the pipe diameter D is 1/9.
Advantages:
The electrostatic sensor we designed possesses many advantages.
- Lots of benefits are in the sensor designed, including simplicity, easy electrical shielding and resistance to mechanical vibration interference.
- Particularly, it is suitable for 3D printing powder feeding pipeline.
- The sensor would be fitted in the harsh industrial site environment.
- The sensor is merely generated the reaction by particles moving, not by depositing.
Therefore, the stability of the sensor is satisfying. It can be adapted in many different conditions. The sensitivity of the sensor is not affected by width of pipe and the thickness as well as chemical nature of particles.
Also read here
how to design and manufacture electrostatic MEMS relay for high power application?