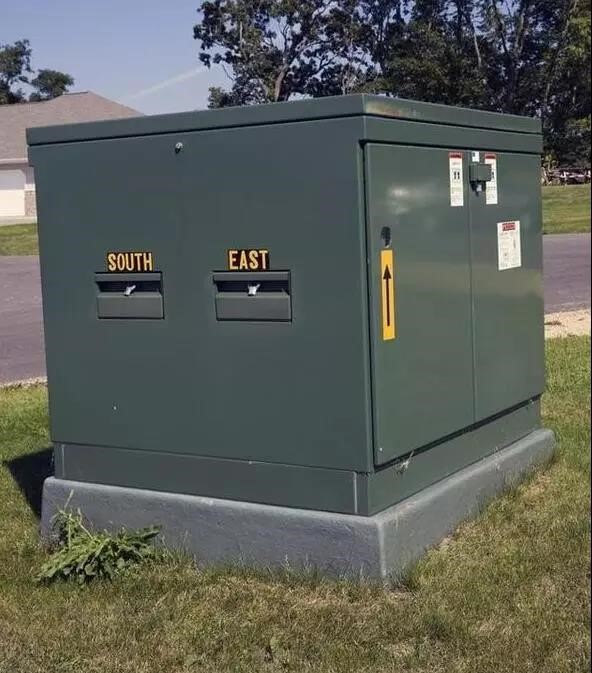
What is Transformer?
The Definition of transformer
A transformer is an electrical device that alters the voltage of an AC circuit, more details see easybom. The notion of mutual inductance is used by the transformer, an AC voltage converter. To satisfy the needs for electrical energy transmission, distribution, and usage, it can convert any voltage value into the voltage value we need at the same frequency. For instance, electricity from a power plant has a lower voltage level and needs to be increased before being sent to a remote place for power consumption. A suitable voltage level must be reached in the power consumption region in order to supply power equipment and everyday electricity. Equipment.
The structural components are the iron core, the primary coil, and the secondary coil. When an alternating current passes through the primary coil and induces a voltage in the secondary coil, an alternating magnetic flux is created in the iron core. An iron core and a coil make up its construction. On the coil, there are two or more windings. The remaining windings make up the secondary winding, which is coupled to the power supply through the primary winding.
The main components of the transformer
-
Iron core
The iron core is one of a power transformer’s most fundamental parts. It follows a “magnetic” trajectory and has a twisted skeleton. On the iron core of the transformer are coiled the main and secondary windings. The portion of the iron core covered by the winding is known as the iron core. A column known as an iron yoke is used to create a closed magnetic circuit by joining the core and column without using windings. The alternating magnetic circuit in the transformer core will induce hysteresis and eddy current loss. The transformer core is typically made of silicon steel sheet with a thickness of 0.3 to 0.5 mm, covered with an insulating varnish that is 0.01-0.13 mm thick on the surface, and laminated after drying in accordance with specific rules, in order to minimize these losses.
-
High and low voltage winding
One of the most fundamental parts of the transformer is the winding. It joins the iron core to create the main body of the power transformer. The transformer’s circuit portion serves as both the conduit for the transformer’s “electricity” and the mechanism that generates the magnetic field and transmits electrical energy.
Based on their diverse arrangement positions, the high and low voltage windings can be divided into two types: concentric and overlapping.
1) Concentric winding
The primary and secondary windings are mounted on the iron core column after being wound into cylindrical coils of varying diameters. The low and high voltage windings are separated using insulating materials. In order to make the extraction of the high voltage windings easier, the low voltage windings are typically placed within. The high-voltage winding is wrapped outside. For large-capacity power transformers with large output currents, the low-voltage winding leads procedure is difficult, and the low-voltage windings are typically located outside the high-voltage windings.
2) Overlap winding
On the same iron core column, high-voltage and low-voltage windings—also known as staggered windings—are alternately arranged with larger gaps, elaborate insulation, and a lot of binding work. The mechanical performance is better, lead wire layout and welding are simpler, and leakage reactance is low, all of which are advantages. Transformers with low voltage and high current frequently employ this material (such as electric furnace transformers, welding transformers, etc.).
-
Tap switch
The voltage regulating switch, sometimes referred to as the tap changer, is a component that modifies the high-voltage winding of the transformer’s tap position. By raising or lowering the number of spins on the primary winding, moving the tap changer can alter the voltage ratio and alter the output voltage. Voltage regulation comes in two flavors: on-load and no-load.
1) Control of no-load voltage
This method of adjusting the number of turns on the primary and secondary windings to carry out step-by-step voltage management while both the primary and secondary windings of the transformer are disconnected from the network is known as non-excitation voltage regulation. Small-capacity transformer tap-changers typically have three positions. Similar to position II, the rated voltage is. When the system voltage is too high, set the tap-changer to position I; when it is too low, set it to position III. To put it another way, “high to high key, low to low key.”
2) Control of on-load voltage
When the transformer is functioning with a load, the tap of the main or secondary winding is adjusted, the number of turns is altered, and the voltage is gradually regulated. Reactance and resistance transition can be used to manage the circulating current while changing taps on an on-load tap changer.
Download the Dimensional Sketch of Transformer here:
-
Gas relay
It is positioned in the middle of the pipe that connects the oil tank and the oil pillow as a protective mechanism against internal transformer flaws and is also known as a Buchholz relay. The gas relay is coupled to the control circuit to produce a gas protection mechanism. A heavy gas protection circuit is created by connecting the lower contact of the gas relay to the external circuit and the higher contact of the gas relay to the signal for light gas. Due to the heavy gas action, the circuit breaker trips and a heavy gas action signal is broadcast.
The laws stipulate that gas relays must be installed on all oil-immersed transformers with a capacity of 800KVA or more as well as factory transformers with a capacity of 400KVA or more.
-
Explosion-proof tube
Since it is a protection device installed to prevent the transformer from deforming when a fault develops inside the transformer, it is also known as a safety airway. It is fixed to the large lid of the transformer. The horn-shaped tube that connects the nozzle to the atmosphere is made of thin film glass plate. or cardboard made of phenol that has been sealed.
-
Oil pillow
It is a system for replenishing and holding oil while the transformer is in use. It is situated above the oil tank at an angle, and oil pipes link it to the tank. To reduce the amount of oil that comes into contact with the air and keep the oil from oxidizing too quickly and getting damp when the volume of the transformer oil expands and contracts with the oil’s temperature, the oil tank can always be filled with insulating oil. The size of the transformer tank is normally one-tenth that of the oil cushion. The upper half of the oil pillow includes an oil injection hole and an air escape flap, and one side of the oil pillow has an oil level indication (oil gauge tube) attached to track changes in the oil level.
-
Respirator
It is additionally known as a moisture absorber. To keep moisture from getting inside the oil pillow, a respirator connects the oil pillow to the outside environment. To maintain the insulating oil in the transformer functioning properly, the respirator contains silica gel, and the desiccant inside the silica gel absorbs moisture and airborne contaminants. The silica gel used in respirators is often color-changing silica gel, which starts out being light blue while dry and gradually turns light red when saturated with moisture. At a high temperature of 120–160°C, the silica gel can now be removed and dried. Keep using the dried even after it becomes blue.
-
Cooling device
The cooling system of an oil-immersed power transformer consists of a radiator and a cooler. A cooler is referred to as having strong oil circulation, whereas a radiator is referred to as having poor oil circulation.
The radiator is created by fitting radiator pipes or fins around the transformer tank. The high-temperature oil around the transformer core can be cooled by the radiator before being returned to the transformer when the transformer is in use because the temperature difference between the top and lower layers of oil allows the oil to flow through the radiator. It decreases the oil tank’s internal transformer working temperature.
-
Thermometer
It is a meter that measures the temperature at which the transformer is functioning. The temperature measurement point is typically on the top layer of the oil. Resistance thermometers, mercury thermometers, and barometer thermometers are all often employed.
Only mercury thermometers should be installed in oil-immersed transformers under 1000 KVA; for oil-immersed transformers 1000 KVA and higher, two forced oil circulation cooling transformers and a thermometer with an alarm signal are required; and for oil-immersed transformers 8000 KVA and higher, two forced oil circulation cooling transformers and a thermometer with an alarm signal are required. For remote temperature measurement, two temperature measurement components must be installed: resistance thermometers and transformers for forced oil circulation cooling.
-
High and low voltage insulation casing
The majority of transformers use porcelain insulating sleeves, which are the primary insulation device used outside the transformer box. The insulating sleeve of the dry-type transformer is constructed of resin. The transformer conducts its high and low voltage windings from the oil tank to the outside through the high and low voltage insulating bushing. The high and low voltage insulation bushing, which also helps to hold the lead and external wire in place, insulates the transformer winding from the earth (shell and iron core). the fundamental components.
Download 11KV Transformer Datasheet from here:
Transformer’s types
Single-phase, three-phase, and multi-phase transformers are available depending on the number of power phases.
There are open transformers, potted transformers, and sealed transformers in accordance with the moisture-proof manner.
Transformers can be classified into the following categories, depending on their intended use: power, voltage regulator, audio, intermediate frequency, pulse, and high frequency.
Transformer’s function
When the power transformer transmits power over long distances, such as when the power is constant, the lower the voltage, the higher the current, the larger the cross-section of the wire, and the higher the line laying cost; if the voltage is increased by a step-up transformer, the line laying cost is reduced. The cost will decrease if the current is decreased. A step-down transformer is needed to change the high voltage into a variety of various voltages that the users can use once it has been delivered to the user center. The transformer is a crucial element of electrical machinery as a result.
What purpose does a transformer serve?
Power transformers and special transformers are the two main categories into which transformers fall.
-
The use of power transformers
A power transformer is one that is used in the power system’s primary circuit for power supply, distribution, and transmission.
1) Increase the voltage
The generator’s insulation level limits the output voltage, which is why it typically ranges between 6.3 and 10.5 kV and never goes above 20 kV. Since the current is substantial while using such a low voltage for long-distance transmission, a lot of electrical energy will be used to overcome the resistance of the transmission line. The generator’s terminal voltage is raised to hundreds of thousands or millions of volts using a step-up transformer in order to lower the transmission current and energy loss on the transmission line without increasing the cross section of the wire. This makes it possible to carry electrical energy far away.
2) Reduce voltage
A step-down transformer is required to reduce the high voltage from the transmission line’s hundreds of thousands or millions of volts to a low voltage that is suitable for electrical device use. In order to turn the high voltage carried by the transmission line into different levels of voltage to meet the needs of diverse loads, a sizable number of step-down transformers are needed in the power supply system.
3) Connect the transmission line
When several power stations are integrated to create a power system, in addition to power transmission lines and other equipment, transformers are needed to connect several lines with uneven voltages.
-
The purpose of special transformers
Transformers used in specialized power supplies, control systems, and telecommunication equipment are known as particular transformers because they have a particular structure, performance, and function.
1) In industrial and mining settings, transformers utilized in rectifiers, electric furnaces, and intermediate frequencies.
2) Look for high-voltage and high-current voltage transformers and current transformers.
3) The voltage regulating transformer and test transformer utilized in the test.
4) Transformers utilized in automatic control systems and automatic equipment, such as control transformers, pulse transformers, audio transformers, etc.
How does a transformer work?
A straightforward single-phase transformer is made of two wires. When a certain amount of current—such as alternating current or pulsed direct current—passes through one of the conductors, a fluctuating magnetic field is produced. When the magnetic field changes, the second conductor will produce a potential difference, according to the electromagnetic mutual inductance theory. A closed circuit produces current when the second conductor is attached to it. After then, the electricity is released. Because a coil’s magnetic field is significantly larger than a straight wire’s magnetic field, a wire (often copper) wound into a coil serves as the relevant conductor in conventional transformers. In general, a transformer is a device that converts impedance, alternating current, and voltage. When an alternating current is delivered via the primary coil, causing a voltage to be generated in the secondary coil, an alternating magnetic flux is created in the iron core (or magnetic core) ( Or current). There is a proportionate link between the voltage VS, VP of the primary and secondary coils and the number NS, NP of the two windings:
The number of turns on both sides of the circuit coils determines the ratio of current or voltage between the two sides of a transformer. The one with more turns has a higher voltage but a lower current, and vice versa. The voltage ratio on each side of the transformer equals the ratio of coil turns on each side when leakage is taken into account, suggesting that the voltage is proportionate to the number of turns.
As a result, the turns ratios of the primary and secondary coils can be altered, altering the voltage in the process. Due to its nature, the transformer is an essential component in voltage conversion. In addition, the transformer won’t be an amplifier because it abides by these two principles, disregarding the impact of leakage.If the voltage on the two sides of the transformer is different and the difference between the two is inversely proportional, then the current flowing through the two sides of the transformer will be different. The side with the lower current will have a greater voltage, and vice versa, if one side of the transformer has a smaller current than the other. However, the power used by both sides of the transformer must be equal (that is, the two values of voltage and current on one side should be multiplied).
How to Use a Transformer?
Using methods:
- Carefully study the transformer’s instruction booklet as well as the manual for the coordinating control box (set) before using the transformer. The grounding wire should be well grounded, and the connecting cable should be attached as instructed in the manual.
- A voltage regulator outputs the AC 220V and 380V power supplies of the dry-type transformer control box (set) to the low-voltage side input end of the transformer. The output is continuously adjustable to the rated voltage after the variable ratio.
- Take into account the reliability of high-voltage testing and the safety of dry-type test transformers to prevent damaging test items or equipment.
- To execute a DC withstand voltage or leakage current test, start by spinning the micro-ampmeter and high-voltage silicon stack on the high-voltage test transformer’s high-voltage output end. Then, gradually raise the voltage to complete the test.
Precautions for the use of transformers:
Due to the electrical distance, three different sounds can be heard during the withstand voltage test: Ionization of the air produces a “cracking crackling” sound. “Zi, zi” is the sound of the air stream. “Slap”: Sparks fly along with the loud, crisp sound of insulation (or air) breaking down. Three portions of the discharged air are typically divided.
The initial stage is ionization. When the electric field is sufficiently large, the air will begin to disintegrate at the enormous point, entering the streamer stage. Theoretically, it satisfies the national standards if it can endure a minute without disintegrating and makes a perfect replica of the “cracking” sound made by cooked beans. The national standard is met if there is a “zi zi” sound but no breakdown for one minute; nonetheless, there is a larger danger of long-term transformer operation with streaming.
The main air passage’s inadequate air distance is the primary cause of the high-pressure noise (high-voltage coil and low-voltage coil). E=U/D E electric field, U voltage, the distance between D electrodes when D is short, E is large, and the air can endure a field strength of 0.7KV/mm under standard air pressure and humidity.
When the electric field is greater than this amount, the molecules are easily ionized. However, if air is not broken down, it will not conduct electricity. The high and low voltage coils have inner and outer layers of insulation as well, therefore composite insulation should be taken into account when determining the insulation of the transformer’s main airway.
The main parameters of the transformer
-
Rated capacity SN
The rated capacity of the transformer refers to the apparent power of the transformer under the rated working condition (rated voltage, rated frequency, and rated use circumstances) specified on the nameplate when the tap changer is positioned in the main tap. The measure is KVA.
Transformer for a single phase, SN=UN2*IN2.
Transformer for three phases, SN=3UN2*IN2.
-
Rated voltage UN1 and UN2
The secondary rated voltage UN2 is the no-load voltage value recorded on the secondary side when the primary side plus the rated voltage is applied. The primary rated voltage UN1 is the grid rated voltage.
The primary and secondary rated voltages of a three-phase transformer serve as a representation of the line voltage.
The rated voltage ratio is the ratio of the main side’s rated voltage to the secondary side’s rated voltage under no-load conditions.
-
Rated current IN1 and IN2
The transformer’s main and secondary rated current is the line current that is permitted to flow through the primary and secondary windings for an extended length of time at the prescribed voltage and rated ambient temperature.
Single-phase transformer IN1=SN1/UN1
IN2=SN2/UN2
Three-phase transformer IN1=SN1/√3UN1
IN2=SN2/√3UN2
-
Impedance voltage
Impedance voltage is another name for short-circuit voltage. In other words, the secondary winding of the transformer is shorted out, and the voltage on the primary winding progressively rises. When the short-circuit current is equal to the rated current, the voltage applied to the primary side is also equal to the rated current.
The identical impedance voltage is one need for the parallel operation of two transformers. The magnitude of the short-circuit voltage value is used to calculate the short-circuit current and determine the relay safety features.
-
No-load current I0
When the secondary side of the transformer is open and the primary side is receiving the rated voltage, the no-load current flows through the primary winding. The capacity of the transformer, the design of the magnetic circuit, and the caliber of the silicon steel sheet all affect how much no-load current there is. The no-load current of a distribution transformer ranges from 3 to 8% of the primary rated current.
-
No-load loss P0
It refers to the power lost by the transformer when it is opened a second time and the rated voltage is applied once. Losses from eddy currents and excitation are included. The manufacturing process and the voltage being used dictate the transformer’s size; the size is unrelated to the size of the load.
-
Short-circuit loss Pk
This is the power that the transformer absorbs while its secondary side is short-circuited and its main winding flows at its rated current. It can display the financial performance of the transformer’s benefits and drawbacks.
-
Temperature rise
The state stipulates that the rise in temperature of the transformer’s upper oil surface cannot be greater than 55°C. To avoid accelerated aging and damage to the transformer oil, the temperature of the top oil surface should not be higher than 85°C.
-
Connection group
The transformer’s connection group serves as a mark for both the windings’ technique of connection on each side of the transformer and the phase relationship of the corresponding line voltage.
1) The name of the connection group
There are two pieces to the connection group label: letters and numbers.
- The preceding letters denote the connection modes of the primary and secondary windings, with uppercase letters denoting the primary winding and lowercase letters denoting the secondary winding’s connection mode, read left to right. While Y or Y is a star connection, D or d is a delta connection. Since there are two types of Y connections—one with a neutral line and the other without—there is no sign indicating that there is no neutral line, and the letter n is placed after the letter Y with a neutral line.
- The value below, which could be an integer between 0 and 11, represents the phase displacement of the secondary winding line voltage to the primary winding line voltage. By dividing by 30°, the secondary winding line is calculated. the number of angles by which the voltage deviates from the phase change of the primary winding line voltage. Line voltages in the primary and secondary windings are in phase if they are zero. The minute hand is made of the line voltage phasor of the primary winding and is positioned at the 12 o’clock position of the clock. The hour hand is made of the line voltage phasor of the secondary winding and is fixed at the 6 o’clock position of the clock. The number indicates how many transformer winding groups there are.
2) Standard connection group
To reduce confusion in manufacturing and use, the national standard stipulates that single-phase dual-winding power transformers have just one connection group and three-phase dual-winding power transformers only have five standard connection groups: Y, yn0, Y, d11, YN, d11, y0, and Y, y0. When both the high and low voltage windings are star-connected, the connection group number is 0, and when the high voltage winding is star-connected but the low voltage winding is delta-connected, it is 11.
Transformer fault type
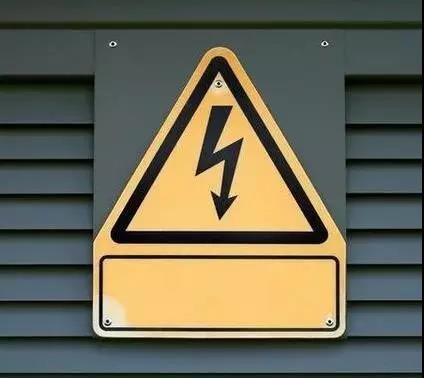
① A problem internal to the fuel tank
The most frequent internal issues with the transformer oil tank are the phase-to-phase short-circuit on each side, the single-phase grounding short-circuit on the high-current system side, and the inter-gate short-circuit between the windings of the same phase.
② A problem external to the gasoline tank
failure of the insulating bushing and a short lead wire at the lead-out end of the transformer group. Ground faults on both the low-voltage and high-current sides, as well as two- and three-phase short-circuit faults.
What kinds of tests should be done during operation of the transformer?
(1) Temperature test.
Regardless of whether the transformer is operating normally or not, its temperature is crucial. The maximum oil temperature is limited by the requirements to 85 degrees Celsius (that is, the temperature rise is 55C). Temperature gauges are frequently included in transformer installations.
(2) Load measurement.
In order to maximize the transformer’s utilization rate and minimize electric energy loss during operation, it is critical to assess the power supply capacity that the transformer can actually provide. A clamp ammeter is used to do the measurement, which is frequently carried out at each season’s peak period of electricity consumption. The value of the current should be between 70% and 80% of the transformer’s rated current. If it exceeds, it means the system is overloaded, and this needs to be fixed immediately.
(3) Voltage measurement.
The requirements require that the voltage variation range be within 5% of the rated voltage. If the voltage rises over this range, a tap should be used to lower it to the acceptable level. The terminal voltage of the secondary coil and the terminal voltage of the terminal user are normally measured with a voltmeter.
(4) Insulating resistance measurement.
To avoid accidents and insulation aging and to maintain constant normal operation of the transformer, the insulation resistance must be evaluated. Attempt to switch the transformer off before taking any measurements. Utilizing a shaker, calculate the transformer’s insulating resistance. At least 70% of the previous measurement must be present in the resistance measurement. When the shaker option is used, the low-voltage coil could be 500 volts.
Types of the Tests performed on Transformers
There are three types of tests performed on the Transformer.
1. Routine Tests
2. Type Tests
3. Special Tests
In Pakistan Transformers are manufactured as per IEC 60076 standards. This standard is applicable in many other countries too.
Also read here