Non magnetic coating ferrous based digital thickness gauge
Non magnetic coating ferrous based digital thickness gauge. Coating of a product is very important to protect the substrate from corrosion, to make it appealing to the eye, to blend the product into the background and to provide surface finish. Since, Coating a product is an expensive process so it should be done carefully. Too much coating can cause the coating to crack as it dries and increase the price of the product, while too little coated material may be inadequate to sufficiently cover the product.
That is why paint/plating thickness is perhaps the most important measurement that is undertaken during the coating process. Due to increasing demand of “Non Magnetic Coating, Ferrous base, Digital Thickness Gauge” in industry, we have selected it as our final year project. By providing cheap coating thickness gauges to Pakistan industry, we can not only help them in controlling the quality of their product but also to decrease the cost per piece.
Non-Magnetic Coating, Ferrous base, Digital Thickness Gauge measures the thickness of non magnetic material coating like zinc, paint, and nickel etc over magnetic material like ferrous and display it on LCD. Our gauge can measure the thickness of nickel coating over ferrous base. Measurement of thickness of coated material is very important in industry since it helps to control the quality of product. During high production portable gauges are best for quality control since other procedures are very time consuming and can’t employed during high production of products in industry.
What is Coating?
To better understand the purpose of our project one should know answer to the questions that Why measures the coating thickness? Why controlling the thickness of coating is the most important factor during quality control of any coated product? To answer this question you need to ask another one – Why are you painting at all? Invariably the answer is one of the following:
- to protect the substrate from corrosion
- to make the product appealing to the eye
- to make the product blend into the background
- to provide a surface finish which is part of the functionality of the product
- to keep radiations of radioactive material inside the storage tank
Coating thickness is suggested by the designer according to the material over which coating is required and purpose of coating. What ever the answer is, coating a product is expensive – especially if you get it wrong.
Disadvantage of Over-Coating:
Too much coated material can cause the coating to crack as it dries.
Disadvantage of Less-Coating:
Too little coated material may be inadequate to sufficiently cover the product and it will have to be re-coated.
That is why paint/plating thickness measurement is perhaps the most important measurement that is undertaken during the coating process.
Scope and Motivation:
Coating thickness gauges are of many types but we have decided to make non magnetic coating, ferrous base, digital thickness gauge because mostly coated material are non magnetic like paint, nickel, zinc, cadmium, powder coating etc. and all of these types of coating are mostly done over iron and steel. In Pakistan, such meters are not available easily in the market. Users have to import it which costs high. Moreover, their maintenance is also a problem due to sensitive technology used in it. If we make such a tester, then not only we can sell our technology to industry but also it will help users of imported non magnetic coating, ferrous base, digital thickness gauge to keep its maintenance locally and it will be cheap. We will make this gauge mainly to test nickel plating thickness over different products since; it can save Pakistan twenty million dollars.
How Pakistan can save two million dollars by manufacturing Nickel Coating Thickness Gauge?
- Pakistan import 1000 ton nickel per year
- 1 ton =1000 kg
- 1 kg costs 2000 Rupees
- Cost of 1000 ton Nickel = 1000× 1000 × 2000 = 2000,000,000 Rupees
- Out of 1000 ton nickel, 500 ton nickel is used for plating/coating
Hence, 500 ton nickel costs 1000,000,000 Rupees
- By doing survey of industries we concluded that 6 % of coated nickel is wasted due to over coating of 1 micron nickel
- 6 % of 1000,000,000 Rupees = 60,000,000 Rupees = $ 7,222,891
- Normally 2 or 3 microns of nickel is wasted (due to over coating) which costs
= $7,222,891 × 3 microns = $ 21,668,673
Coating Thickness Gauge Technology:
There are various technologies through which Coating thickness gauges are manufactured. On the basis of shown output technology Coating thickness gauges can be classified as
Analog:
If the gauge shows the thickness of coating in analog form i.e by moving the needle along the scale then it is called analog.
Digital:
If the gauge shows the thickness of coating in digital form i.e. in the form of digits on LCD or 7-segment display then it is called digital gauge.
The Coating thickness gauge can also be classified on the basis manufacturing technology as Mechanical and Electrical.
Mechanical:
In mechanically manufactured gauges a magnet is attached to one end of a pivoting balanced arm and connected to a calibrated hairspring. By rotating the dial with a finger, the spring increases the force on the magnet and pulls it from the surface. These are usually analog and called roll-back type meter.
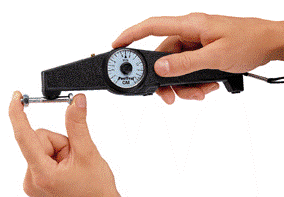
Electrical:
In electrically manufactured meters principle of magnetic field induction is used. They are usually analog meters as shown in fig. Our gauge is also of this type.
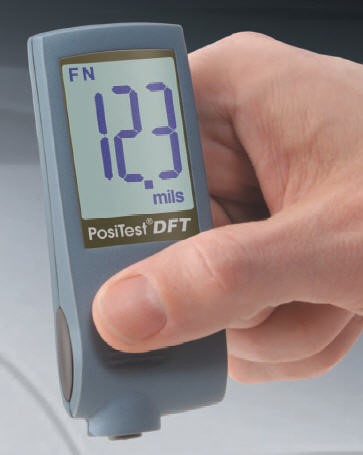
Gauge technology:
The technology which we are using in our Non-Magnetic Coating, Ferrous Base, Digital Thickness Gauge is the base of all types of non-magnetic coating measuring instruments. The difference is only in the calibration of scale or in the programming of microcontroller. The relationship which magnetic field sensor shows about that particular coating is observed by plotting a graph between coating thickness in microns and output voltage of sensor. The equation of that graph is then programmed in microcontroller. Gauge technology and Calibration process is explained in the next chapter by considering nickel as coating. By following those steps one can make gauge to measure any non-magnetic coating over ferrous. Some commonly use coating thickness gauges are
Zinc Coating thickness gauge
Zinc metal has a number of characteristics that make it well-suited for use as a coating for protecting iron and steel products from corrosion. Its excellent corrosion resistance in most environments accounts for its successful use as a protective coating on a variety of products and in many exposure conditions. The excellent field performance of zinc coatings results from their ability to form dense, adherent corrosion product films and a rate of corrosion considerably below that of ferrous materials, some 10 to 100 times slower, depending upon the environment Zinc plating involves the electrolytic application of zinc by immersing clean steel parts in a zinc salt solution and applying an electric current. This process applies a layer of pure zinc that ranges from a few microns on cheap hardware components to 15 microns or more on good quality fasteners. Technical and cost issues prevent the economical plating of components with heavier coatings.
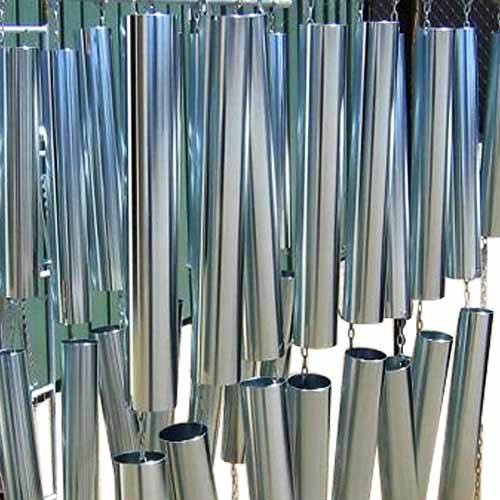
The Sikel production line incorporates a thickness gauge. This appliance enables fast and accurate measurement of the thickness of the zinc or zinc/nickel coating on the steel strip. Measurement is performed on-line, during the production process, without making contact with the steel strip and with a high level of accuracy and reliability.
Enamel Coating Tester
The oil based paint is called enamel. Enamel paint can withstand more damage but it is not easily removable. It is commonly done over doors and windows. High temperature enamel paint is done over engines, brakes and exhaust. This process requires specified thickness of coating so that it will withstand high temperature with ought cracking and rust. It quality control requires enamel coating thickness gauge.
Nickel Coating Tester
Nickel-containing materials make major contributions to many aspects of modern life, but these often go unrecognized. The list is very long, and includes applications in buildings and infrastructure, chemical production, communications, energy supply, environmental protection, food preparation, water treatment and travel. All these areas rely, to some degree, on nickel’s unique combination of properties. Nickel electroplating can also be used to make items by building up thick deposits on a substrate. A major application of electroless nickel today is in computer hard discs. Nickel’s resistance to corrosion is one of its most valuable properties. The estimated annual cost of corrosion in the U.S.A. alone is $300 billion equivalent to 4% of gross national product. Far and away the largest use of nickel alloys is in the area of corrosion prevention. Production of Electroplated parts requires coating thickness control to control the quality and cost of the product. This requires a portable nickel coating thickness tester.
Latex Paint Coating Tester
Latex paint is a water-based paint. For that reason, it is much cheaper than the oil-based enamel paint. Latex paints are most commonly used for the interior walls of a house.
Powder coating is the type of paint coating. Powder coating is the technique of applying dry paint to a part. The final cured coating is the same as a 2-pack wet paint. In normal wet painting such as house paints, the solids are in suspension in a liquid carrier, which must evaporate before the solid paint coating is produced. In powder coating, the powdered paint may be applied by either of two techniques.
- The item is lowered into a fluidized bed of the powder, which may or may not be electrostatic ally charged, or
- The powdered paint is electro statically charged and sprayed onto the part.
The part is then placed in an oven and the powder particles melt and coalesce to form a continuous film.
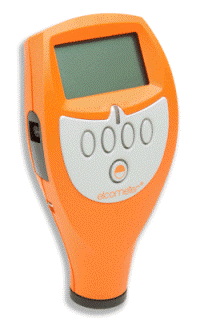
Non-destructive test methods are required to determine powder coating thickness on both metallic and non-metallic substrates such as medium density fiberboard (MDF). Powder Coating inspectors often need a means to verify the thickness of parts as early as possible into the coating process. This may require the immediate measurement of hot parts as they come out of the oven, or even the measurement of applied powder thickness prior to curing. For this purpose a portable powder coating thickness tester is used.
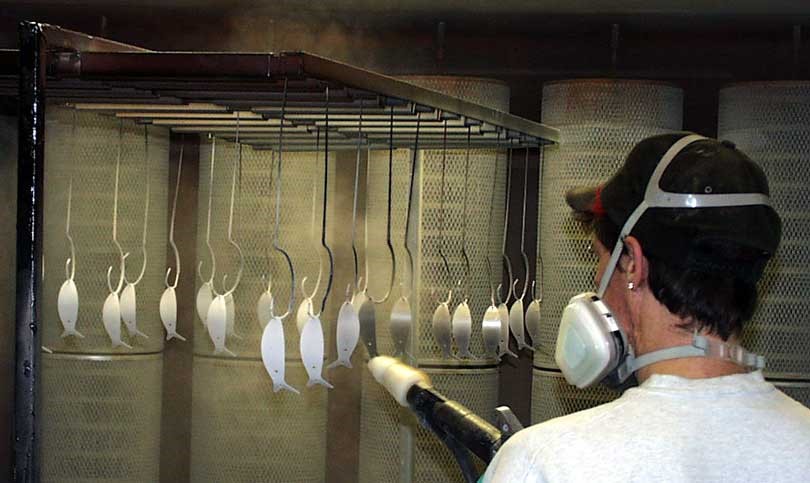
Coating Thickness Tester
Nickel Coating Thickness Tester
Nickel-containing materials make major contributions to many aspects of modern life. The list is very long, and includes applications in buildings and infrastructure, chemical production, communications, energy supply, environmental protection, food preparation, water treatment and travel.
Nickel electroplating is extremely well-known and widely applied. The technique has long been used to provide both corrosion-resistant and decorative finishes, and is also used to create the substrate for chromium coatings. Nickel provides the corrosion resistance and lustrous appearance. Electroplated nickel product’s cost is controlled by controlling the amount of nickel deposited over product. This can be done only by measuring the nickel coating done over product during production. Nickel Coating thickness Tester is used for this purpose.
Also read here
https://eevibes.com/electronics/electronic-circuits/real-time-object-detection-and-tracking/